Manufacturing Process
Quality born from advanced technology
・
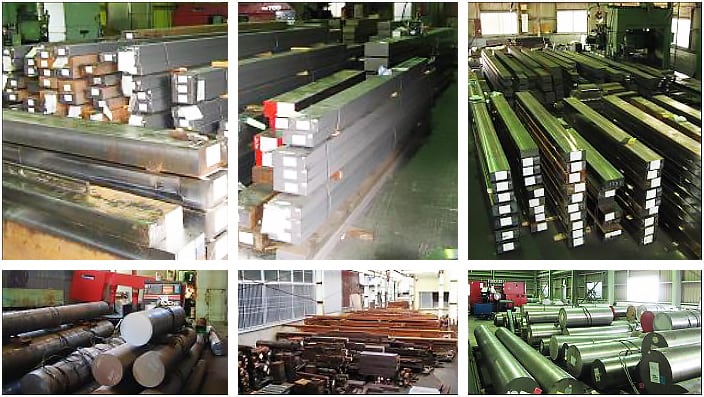

Material Selection
Selection of the optimal steel grade based on proven experience and expertise
Based on the shearing specifications, we select the optimal steel grade from a wide range of materials,
including wear-resistant steel and tough steel. The selection process takes into account the conditions of the materials
to be sheared, past performance, and other relevant factors. Our blade steels are primarily based on die steel and high-speed steel, with proprietary steel grades available.

Cutting, Forging, Annealing
Considering the dimensions and materials, we select the optimal processing method.
We perform material cutting with consideration for product dimensions, machining allowances, and grinding allowances.
For large blades and other components requiring forging, we consider the weight before cutting. For straight blades, we choose between rolled material or forged material for cutting. For circular blades, we decide between using round bars or forging before cutting.
After forging, we conduct annealing to adjust hardness and refine the material structure.
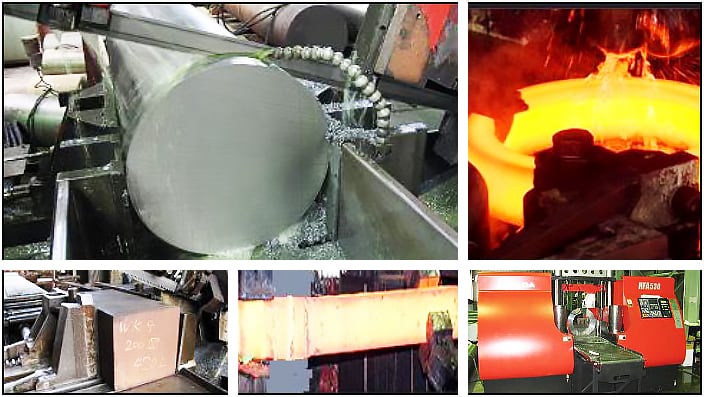
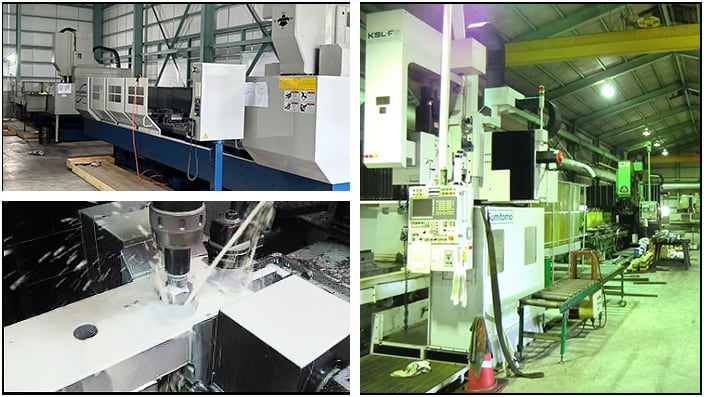

Machining
We adjust for dimensional changes caused by heat treatment and accommodate various conditions.

Heat Treatment
A crucial process that is key to the performance of the blade.
Heat treatment is a critical process that is key to the performance of the blade.
By maintaining a consistent temperature distribution during heating and cooling,
we minimize variations in hardness. The heating pattern and cooling method are adjusted according to the steel grade and specified hardness.
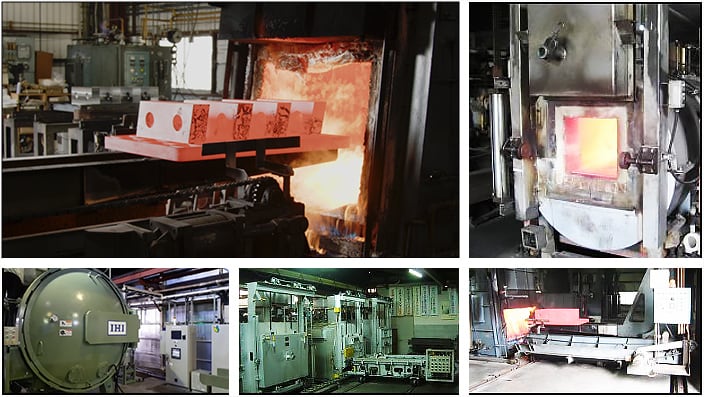
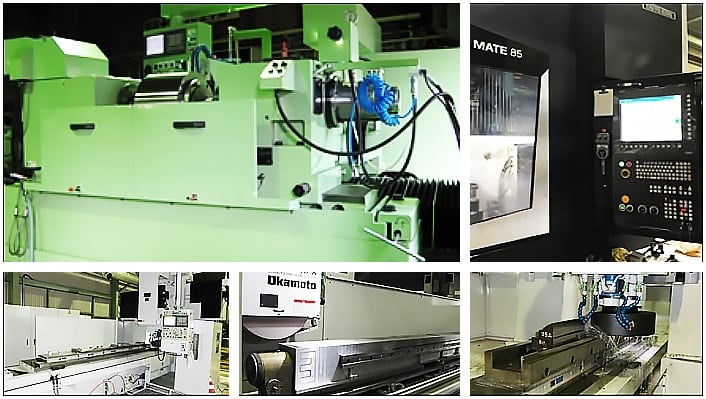

Grinding Process
The final grinding process imparts sharpness to the shearing blade.
The grinding process is the final stage of blade manufacturing, where we utilize the latest equipment and grinding techniques to achieve the desired dimensional tolerances and precision. For each steel grade and specified surface roughness,
we select the appropriate grinding wheel and set the optimal grinding conditions, ensuring that the shearing blade is given its sharpness.

Wire EDM & Surface Treatment
Surface treatment enhances the properties of the blade.
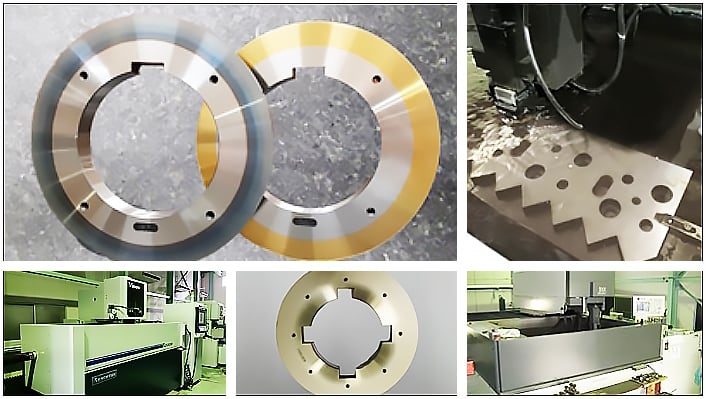
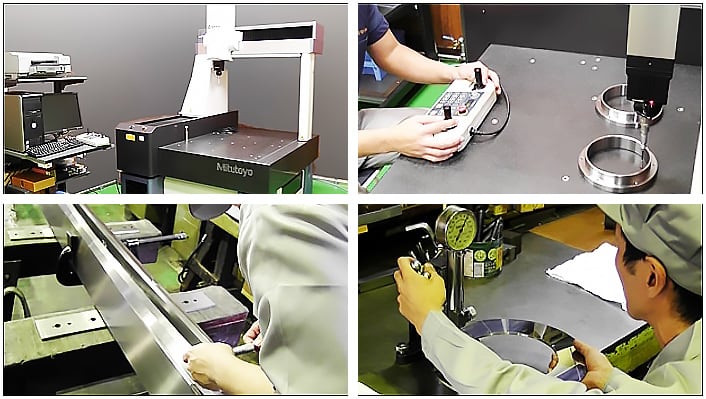
